How To Build a Business Case For Predictive Maintenance
.jpg)
Ensuring equipment reliability while controlling maintenance costs is a challenge that manufacturers continue to face. As production lines become increasingly complex and efficiency demands soar, traditional maintenance practices often falls short, resulting in both unplanned downtime and unnecessarily high maintenance expenditures.
This has driven a significant shift toward predictive maintenance, an intelligent solution that harnesses data analytics, artificial intelligence, and machine learning to forecast equipment failures before they occur. By understanding both visible and hidden maintenance costs, companies can optimize asset performance, extend machinery lifespan, and achieve a strong return on investment.
This blog explores the true cost of outdated maintenance practices, highlighting how predictive maintenance reveals hidden inefficiencies while delivering measurable returns. We will also discuss key implementation strategies, critical success factors, and practical steps for building a compelling business case for proactive machine maintenance in your organization.
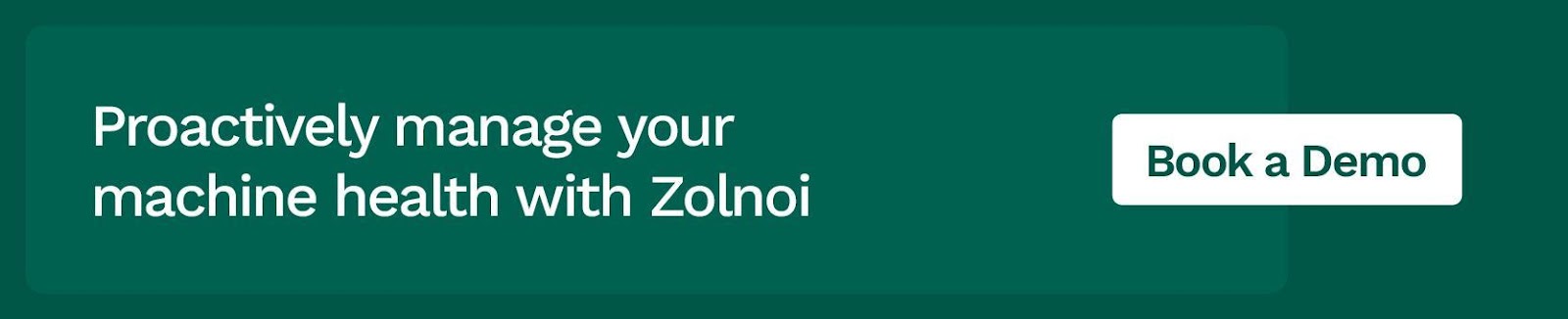
Unveiling the Iceberg of Maintenance Losses
Machine maintenance costs in manufacturing often extend far beyond what meets the eye, much like an iceberg. The visible expenses are only a tiny fraction of the total impact, while hidden beneath the surface are less obvious losses that quietly erode profitability.

Visible Costs: The Tip of the Iceberg
The immediately apparent costs of machine maintenance include:
- Direct repair costs: When equipment fails, the immediate outlay on parts and labor is evident. Unexpected failures can result in expensive repairs and production delays that compound overall maintenance expenses.
- Replacement parts: The cost of acquiring specialized components for machinery can escalate quickly. Frequent replacements, especially when expedited shipping or specialized services are required, further strain maintenance budgets.
- Unplanned Downtime: Perhaps the most significant visible cost, unplanned downtime, can be devastating. In the petrochemical industry, for instance, manufacturers can lose up to $260,000-$2 million for every unexpected shutdowns.
Hidden Costs: The Bulk Beneath the Surface
While visible costs are substantial, the following hidden costs can often overshadow them:
- Reduced Equipment Life: Improper or inadequate maintenance accelerates wear and tear, shortening the lifespan of valuable assets. Common examples include premature compressor failure, deteriorating bearings in conveyor systems, and worn-out gearboxes.
- Safety Risks: Poorly maintained equipment increases the likelihood of accidents and health hazards. The US Department of Labor estimates that machine-related accidents cost companies $11 billion annually in workers’ compensation and lost productivity.
- Quality Issues: Equipment malfunctions often lead to defects and rework, impacting product quality and customer satisfaction. These issues can damage your reputation and lead to lost business opportunities.
- Operational Inefficiencies: Suboptimal performance of machinery results in productivity losses. 80% of manufacturing plants cite aging equipment or machine breakdowns as the leading cause of operational inefficiency.
- Compliance Penalties: Faulty equipment can lead to regulatory non-compliance. Depending on the severity and frequency of the infractions, fines for safety violations can range from thousands to millions of dollars.
Understanding Predictive Maintenance
Predictive maintenance (PdM) represents a step change from the traditional maintenance practices. Unlike preventive maintenance, which follows a fixed schedule regardless of equipment condition, PdM relies on continuous monitoring and data analytics to predict when maintenance should occur.
How PdM Differs from Traditional Maintenance Methods?
To fully appreciate the benefits of predictive maintenance, it is essential to understand the approach of different conventional maintenance strategies. They are as follows:
- Reactive Maintenance: This strategy addresses equipment issues after they occur. While this is simple to implement, it can lead to significant production losses and increased maintenance expenses.
- Preventive Maintenance: This method follows a fixed schedule regardless of equipment condition. While it helps prevent some breakdowns, it can lead to unnecessary maintenance activities and potential over-servicing.
- Condition-Based Maintenance: This approach monitors equipment and triggers maintenance when specific indicators show signs of decreasing performance. Although more efficient than preventive maintenance, it may not provide enough lead time for optimal planning and can still result in unexpected downtime.
Predictive Maintenance uses data analytics and machine learning to predict future failure points and performance issues. It optimizes maintenance scheduling, minimizes downtime, and extends equipment life, offering a more comprehensive solution to maintenance challenges.
Addressing issues proactively significantly reduces unplanned downtime. A research by Deloitte shows that Predictive Maintenance can reduce breakdowns by 70% and downtime by 50%, leading to substantial improvements in operational efficiency.
Implementing proactive maintenance strategies also contributes to energy efficiency by ensuring equipment operates at optimal levels. It reduces waste from premature part replacements and minimizes the carbon footprint associated with emergency repairs.
How Does Predictive Maintenance Reduce Maintenance Losses?
Predictive Maintenance (PdM) offers a strategic advantage by significantly reducing maintenance losses across various dimensions of industrial operations.
- Improved Machine Availability: Predictive maintenance significantly enhances machine availability by detecting potential issues early, preventing unexpected breakdowns that can disrupt production. This proactive approach ensures equipment runs reliably, supporting continuous operations without last-minute interruptions. As a result, manufacturers experience higher overall equipment effectiveness (OEE) and maintain consistent output without sacrificing efficiency.
- Targeted Cost Reduction: This strategy reduces maintenance costs by focusing on condition-based interventions. Instead of routine, fixed-interval servicing that may replace components prematurely, data-driven maintenance extends component life and reduces material waste. Industry reports suggest cost savings between 10% and 30% for organizations that adopt PdM strategies.
- Energy Savings: By optimizing equipment performance, PdM contributes to significant energy savings. Well-maintained machines operate more efficiently, consuming less energy and reducing operational costs.
- Quality Impact: Maintaining machinery within ideal operating parameters enhances product quality and reduces defects. With fewer production errors and rework incidents, organizations save on both material costs and labor, further solidifying the business case for PdM.
Beyond measurable gains, PdM offers intangible benefits that enhance overall operations.
- Proactive maintenance minimizes safety risks, creating a safer work environment.
- By ensuring equipment aligns with industry standards, PdM supports regulatory compliance, avoiding costly penalties.
- Reliable operations lead to improved customer satisfaction, as consistent service delivery builds trust and loyalty.
Predictive Maintenance in Action: Quantifying Downtime Savings for Critical Gearbox Assets
Consider a scenario involving a critical asset like a gearbox with multiple failure modes. Suppose a maintenance manager identifies ten potential issues causing downtime, with each issue resulting in an estimated loss of 10 operational hours per year, which translates to a total of 100 lost hours. If a predictive maintenance system can address eight of these issues with a 95% success rate, the potential downtime savings can be calculated as follows:
- Identified Issues Addressed: 8
- Total Potential Downtime Saved: 8 issues × 10 hours each = 80 hours
- Effective Savings at 95% Success: 80 hours × 0.95 = 76 hours saved per year
As explained in the previous section, there are other benefits across energy, quality, maintenance costs, etc., which can also be quantified. For example, one of our customers identified that during downtime, the auxiliaries are still running, and there is substantial energy waste. When quantified, that was substantial enough to cover the cost of the solution.
Maintenance managers can adapt this framework to their specific environments by analyzing historical data and using expert judgment to refine their cost-benefit analyses.
Critical Success Factors for Implementing Predictive Maintenance
Implementing Predictive Maintenance (PdM) successfully requires careful consideration of the following critical success factors:
- Machine Criticality Assessment: This process involves identifying and prioritizing assets based on their impact on operations. It serves as the foundational step in developing effective maintenance strategies, ensuring that resources are allocated to the most critical equipment. Here is how you can do the assessment:
- Step #1: Catalog all machinery and equipment within the organization.
- Step#2: Analyze potential failure modes and their consequences.
- Step#3: Assess the impact of each asset’s failure on safety, production, costs, and compliance.
- Step#4: Rank assets to focus maintenance efforts where they are most needed.
- Data Quality and Integration: The success of a PdM system hinges on the quality and reliability of the data it uses. Integrate sensors, historical logs, and maintenance records to create a robust data framework. High-quality, integrated data enables accurate forecasting and informed decision-making, ensuring that predictive maintenance delivers on its promise.
- Technology Selection: Choosing the right predictive maintenance technology is crucial. Evaluate solutions based on:
- Applicability: The technology’s relevance to your specific asset types and operational needs.
- Scalability: The ability to expand across a diverse range of equipment.
- Integration: How smoothly the solution integrates with your existing IT infrastructure. Selecting a vendor that provides ongoing support and training can further enhance the success of your PdM initiative.
- Organizational Readiness: Implementing predictive maintenance requires a cultural shift. Invest in training programs to ensure that all stakeholders, from maintenance technicians to management, understand and embrace the new processes. Align traditional maintenance procedures with the predictive model and create an environment of ongoing learning and refinement.
- Implementation Roadmap and Pilot Testing: Begin with a pilot project focused on a critical asset or production line. This approach allows you to use pilot insights to refine predictive algorithms and develop a phased roadmap that minimizes risk and disruption during full-scale deployment.
Building a Business Case for Predictive Maintenance
Creating a compelling business case for Predictive Maintenance involves a strategic approach that addresses current challenges and aligns with organizational goals.
1. Identify Current Maintenance Challenges
Start by gathering data on existing maintenance issues to establish a baseline for improvement. This step is crucial for understanding your current situation.
- Calculate total hours and cost of unplanned downtime.
- Break down maintenance costs, including direct and indirect expenses.
- Assess risks associated with equipment failures, focusing on safety and compliance.
By thoroughly analyzing these aspects, you will be able to create a robust foundation for your predictive maintenance business case.
2. Align PdM with Organizational Goals
Show how predictive maintenance supports company objectives to gain management support. This alignment is key to securing approval for implementation.
- Show how reducing downtime aligns with production targets and improves OEE.
- Estimate cost savings from reduced emergency repairs and extended asset lifespan.
- Highlight potential for increased customer satisfaction and market share due to improved reliability.
Linking PdM to strategic goals strengthens your case and increases the likelihood of approval from decision-makers.
3. Conduct a Cost-Benefit Analysis
Develop a clear financial model that outlines the investment required and potential returns. This analysis will help justify the expenditure.
- Detail initial investment costs for PdM technology, including sensors, software, and training
- Project savings from reduced downtime, decreased maintenance costs, and improved energy efficiency
- Calculate ROI and payback period to demonstrate the financial viability of PdM
A comprehensive cost-benefit analysis provides concrete evidence of PdM's value to your company.
4. Define Key Performance Indicators (KPIs)
Establish measurable metrics to track the success of your PdM implementation. These indicators will help you monitor progress and demonstrate results.
- Focus on reducing unplanned downtime and increasing the mean time between failures.
- Track the decrease in maintenance costs and improvement in overall equipment effectiveness.
- Monitor energy savings and extended asset lifespan attributable to PdM.
Well-defined KPIs provide tangible evidence of PdM's success and help justify ongoing investment in the program.
5. Outline Implementation Strategy
Provide a clear roadmap for PdM adoption to show management you have a practical plan. This strategy demonstrates your readiness to execute the project.
- Start with a pilot project on critical assets, setting specific goals and timelines.
- Outline phases for full implementation, prioritizing based on criticality and potential ROI.
- Identify necessary resources, including personnel requirements and additional tools or training.
A well-thought-out implementation plan instills confidence in the feasibility of your PdM proposal.
6. Address Potential Challenges and Summarize Benefits
Anticipate common concerns and provide solutions to show you have considered all aspects. Conclude with a powerful summary of PdM advantages.
- Address data security, system integration, and cultural change concerns.
- Outline plans for staff buy-in and adoption of new processes.
- Summarize key benefits such as reduced downtime, lower costs, extended asset life,and improved safety and efficiency.
By addressing challenges and highlighting benefits, you can present a comprehensive and persuasive case for PdM implementation.
Conclusion
Predictive maintenance (PdM) effectively addresses both the visible and hidden costs associated with equipment upkeep. Proactively monitoring machinery, reduces direct expenses like repair costs and unplanned downtime while also mitigating hidden costs such as energy waste, quality issues, and operational inefficiencies.
Zolnoi stands out as an industry leader in predictive maintenance solutions, offering a unique blend of expertise and innovation. Focusing on maximizing energy savings and improving production efficiency, we employ cutting-edge AI algorithms developed over five years of research. Our solutions outperform traditional methods, providing clients with unparalleled accuracy and reliability in maintenance predictions.
If you are thinking of implementing predictive maintenance in your factory, book a quick demo with our team, and we will be happy to help.