Top 10 Industrial Maintenance KPIs to Maximize Equipment Uptime
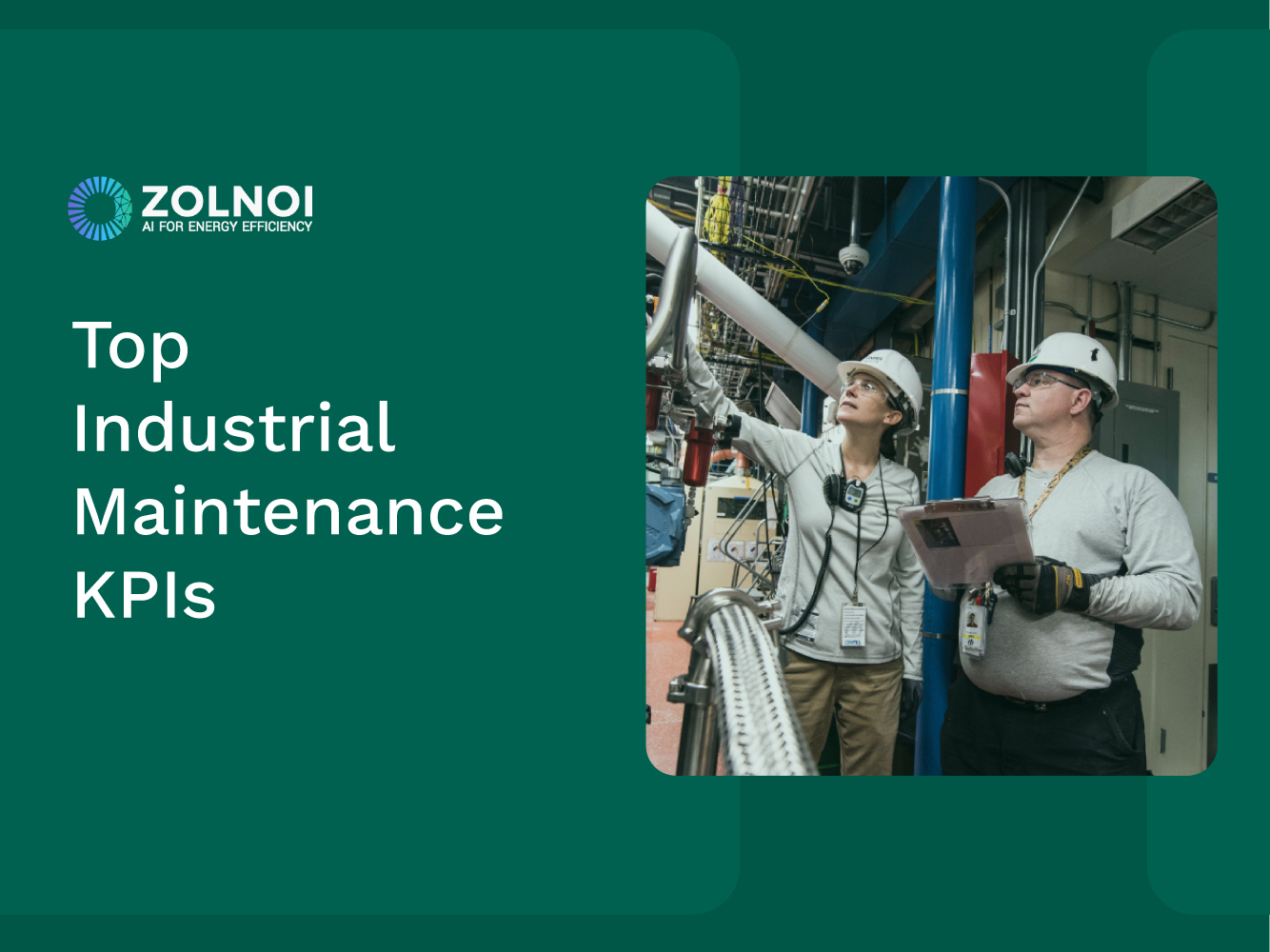
In manufacturing, equipment health has become much more than a maintenance concern and is considered the key to operational excellence and long-term profitability. Effective maintenance strategies boost productivity, minimize downtime, and safeguard your bottom line. To achieve this, manufacturers rely on Key Performance Indicators (KPIs) that offer deep insights into machine conditions and drive process efficiency.
In the current Industry 4.0 landscape, advanced analytics and IoT sensors have streamlined KPI tracking, providing real-time data and predictive insights, enabling you to address equipment issues before they impact production. This proactive approach enhances equipment reliability, improves worker safety, and supports data-driven decision-making.
This blog explores ten critical KPIs for equipment health, showing you how to harness these measurement tools to streamline your maintenance strategy and drive operational excellence.
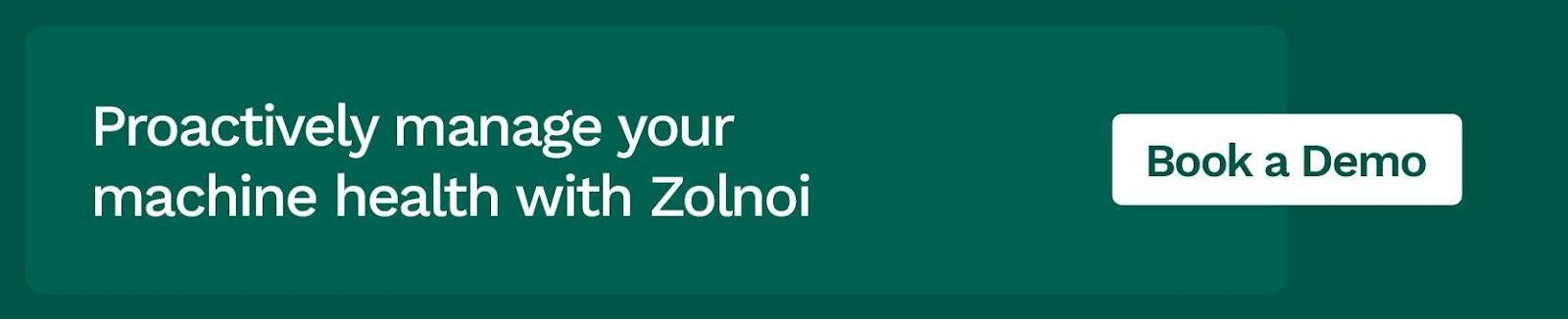
10 Critical KPIs for Equipment Health
Tracking the right Key Performance Indicators (KPIs) is crucial for maintaining optimal equipment health in manufacturing. Here are 10 essential KPIs that can help transform your maintenance strategy.
Mean Time Between Failure (MTBF)
Mean time between failure (MTBF) measures the average time between equipment failures, indicating your machinery’s reliability. You can calculate it by dividing the total operational time by the number of failures over a specific period.
MTBF = Total Operational Time / Number of Failures
A higher MTBF suggests better equipment reliability and the effectiveness of your maintenance practices. Tracking MTBF helps identify patterns in your equipment failures, allowing for targeted improvements. It guides resource allocation for maintenance and informs decisions on equipment replacement or upgrades. Operators often track it on a monthly basis for consistent reliability insights and timely process improvements.
Mean Time to Repair (MTTR)
MTTR represents the average time required to repair and restore equipment to full functionality after a failure. It is calculated by dividing the total repair time by the number of repairs over a specific period.
MTTR = Total Repair Time / Number of Repairs
A lower MTTR indicates more efficient maintenance processes and quicker response times. Monitoring MTTR helps you assess the effectiveness of your maintenance team and procedures. It highlights areas for improvement in repair processes, spare parts management, and technician training. By reducing overall repair time, you can control labor expenses and protect vital production schedules.
Overall Equipment Effectiveness (OEE)
Overall equipment effectiveness is a comprehensive metric that combines availability, performance, and quality to measure overall equipment productivity.
OEE = Availability x Performance x Quality
Where:
- Availability = Actual Production Time / Planned Production Time
- Performance = (Ideal Cycle Time x Total Count) / Actual Production Time
- Quality = Good Count / Total Count
A higher OEE indicates more efficient equipment utilization and production processes. Tracking this metric provides a holistic view of your equipment’s performance. It helps identify bottlenecks in your production process and areas for improvement. By breaking down the OEE into its components, you can pinpoint specific issues affecting productivity. This will help identify whether they are related to equipment downtime, slow production rates, or quality defects.
Planned Maintenance Percentage (PMP)
PMP measures the proportion of maintenance activities that are planned versus unplanned. It is calculated by dividing planned maintenance time by total maintenance time and multiplying by 100.
PMP = (Planned Maintenance Time / Total Maintenance Time) x 100
A higher PMP indicates a more proactive maintenance strategy, which typically leads to better equipment reliability. Monitoring PMP helps you shift from reactive to proactive maintenance. It encourages better planning and scheduling of maintenance activities, reducing unexpected breakdowns and associated costs. A high PMP often correlates with improved equipment lifespan and an efficient use of maintenance resources.
Asset Utilization
This metric measures how effectively you are using your equipment compared to its potential. You can calculate it by dividing actual output by the maximum possible output over a given period.
Asset Utilization = Actual Output / Maximum Possible Output
Higher asset utilization suggests more efficient use of your equipment and resources. Tracking this KPI helps you identify underutilized equipment and opportunities for increased productivity. It can guide decisions on production scheduling, capacity planning, and equipment investments. Improving asset utilization can lead to higher output without additional capital expenditure.
Specific Energy
It measures the amount of energy your equipment uses during operation per production unit. You can calculate it by dividing the total energy used by the production output over a specific period.
Specific Energy = Total Energy Used / Production Output
Lower specific energy indicates more efficient equipment operation. Tracking this KPI helps you identify energy-intensive processes and equipment. It guides efforts to reduce energy costs and improve sustainability. By monitoring energy consumption trends, you can detect anomalies that might indicate equipment issues, allowing for timely interventions.
Maintenance Cost as Percentage of Replacement Asset Value (RAV)
This KPI measures the cost-effectiveness of your maintenance program relative to the value of your assets. It is calculated by dividing the total maintenance cost by the replacement asset value and then multiplying it by 100.
Maintenance Cost % of RAV = (Total Maintenance Cost / Replacement Asset Value) x 100
A lower percentage typically indicates more cost-effective maintenance practices. Tracking this KPI helps you assess the efficiency of your maintenance spending. It provides context for maintenance costs and helps with budget decisions. By comparing this metric across different assets or facilities, you can identify areas where maintenance practices might need improvement.
Maintenance Schedule Compliance
This KPI measures how well your team adheres to planned maintenance schedules. You can calculate it by dividing the number of completed scheduled maintenance tasks by the total number of scheduled tasks and then multiplying by 100.
Maintenance Schedule Compliance = (Completed Scheduled Maintenance Tasks / Total Scheduled Maintenance Tasks) x 100
Higher compliance indicates better adherence to preventive maintenance plans. Tracking this KPI helps ensure that preventive maintenance is carried out as planned. It can highlight issues with resource allocation or scheduling. Improved maintenance schedule compliance often leads to fewer unexpected breakdowns and extended equipment life.
Downtime to Operating Time Ratio
This KPI measures the proportion of time equipment is non-operational due to breakdowns or maintenance. You can calculate it by dividing the total downtime by the total operating time over a specific period.
Downtime to Operating Time Ratio = Total Downtime / Total Operating Time
A lower ratio indicates better equipment availability and reliability. Tracking this KPI helps you understand the impact of equipment failures and maintenance activities on production. It can guide efforts to improve equipment reliability and maintenance efficiency.
Mean Time to Failure (MTTF)
MTTF measures the average time a non-repairable component or system is expected to last before failing. You can calculate it by dividing the total operating time by the number of failed units.
MTTF = Total Operating Time / Number of Units
A higher MTTF indicates better reliability and longer-lasting components. Tracking this metric helps predict when components are likely to fail, allowing for proactive replacement. By comparing MTTF across different brands or models, you can make more informed purchasing decisions for replacement components.
How to Implement an Effective KPI Monitoring System
Follow this strategic roadmap to establish a data-driven maintenance approach for your manufacturing facility.
- Assessment: Start by evaluating your current asset conditions and KPI tracking capabilities. Conduct a thorough audit of your equipment, existing data collection methods, and reporting systems. Identify gaps in your monitoring processes and areas where you lack visibility into equipment performance.
- KPI Selection: Choose KPIs that align with your company’s goals and reflect the criticality of your equipment. Consider factors such as production targets, cost reduction objectives, and regulatory requirements. Prioritize KPIs that provide actionable insights and directly impact your bottom line.
- Technology Integration: Implement IoT sensors and data collection systems to capture real-time equipment data. Deploy analytics platforms that can process and visualize this data effectively. Ensure your technology stack can handle the volume and variety of data you will be collecting across your facility.
- Baseline Development: Using historical data and industry standards, establish performance benchmarks for each KPI. These benchmarks will serve as reference points for measuring improvement and identifying anomalies. Consider seasonal variations and production cycles when setting these benchmarks.
- Staff Training: Empower your teams to interpret KPI data and take appropriate actions. Provide training on data analysis techniques and the use of new monitoring tools. Encourage a data-driven culture where decisions are based on KPI insights rather than gut feelings.
- Continuous Improvement: Regularly refine your KPI targets, monitoring strategies, and maintenance processes based on data insights. Set up a review cycle to assess the effectiveness of your KPIs and adjust as needed. Use advanced analytics to uncover hidden patterns and optimize your maintenance approach continuously.
Final Thoughts
Monitoring the right KPIs helps you improve equipment performance, reduce downtime, and maintain a steady rhythm across your production cycle. These metrics go beyond tracking to support stronger execution and faster decisions across maintenance operations.
As manufacturers adopt Industry 4.0 principles, the shift from reactive metrics to predictive, data-driven insights becomes critical. KPIs, powered by real-time data and advanced analytics, give you the foresight to act early, optimize asset usage, and protect margins in a highly competitive market.
At Zolnoi, we believe that intelligent machine maintenance is the foundation of sustainable manufacturing. Our AI-powered platform combines sensor intelligence, machine learning algorithms, and deep industrial expertise to turn raw machine data into actionable insights. We go beyond system dashboards to help you build resilient and self-optimizing operations.
We partner with forward-looking manufacturers who want to unlock measurable value from their data. If you are ready to move toward a smarter maintenance approach, we are here to support your journey.
Book a consultation with our team today, and we will help you design a KPI monitoring strategy that delivers long-term value.